What Grade Of Stainless Steel Is Best For Coastal Highway Guard Rails And Barriers?
Coastal infrastructure faces unique challenges due to constant exposure to salt spray and marine environments that can accelerate the corrosion of metal structures. When protecting motorists and pedestrians, choosing the right material for guard rails and barriers is crucial. What grade of stainless steel is best for coastal highway guard rails and barriers?
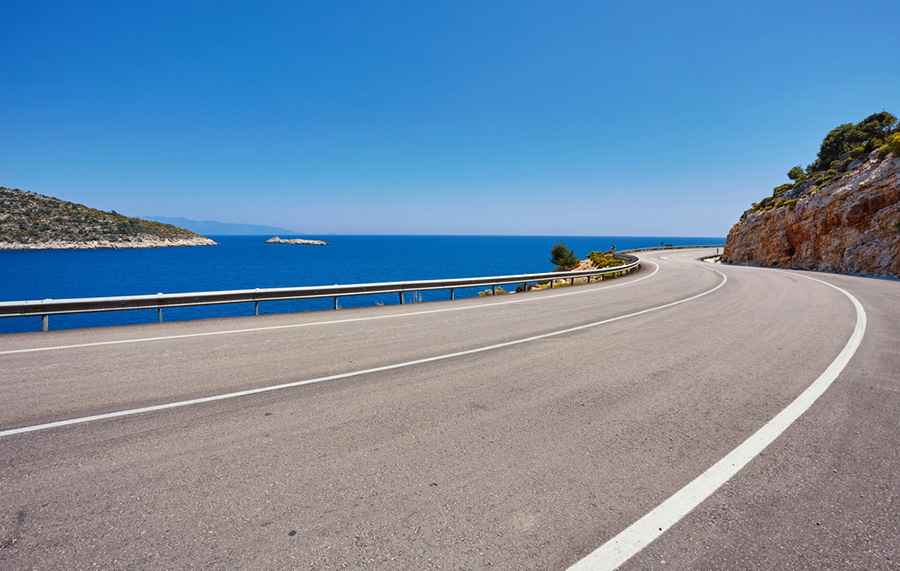
Grade 316 stainless steel is the optimal choice for coastal highway guard rails and barriers due to its superior corrosion resistance in marine environments. It contains 2-3% molybdenum, which provides enhanced protection against chloride attack.
While this answer is straightforward, it's important to continue reading because several other grades of stainless steel might be suitable, depending on specific environmental conditions and budget constraints. Understanding these alternatives could help you make a more cost-effective decision while maintaining safety and durability standards.
What Other Stainless Steel Grades Are Suitable For Coastal Barriers?
While Grade 316 is the gold standard, Grade 304 stainless steel can be a viable alternative in less severe coastal environments, particularly areas several miles inland from direct ocean spray. Grade 304 contains 18% chromium and 8% nickel, providing good corrosion resistance at a lower cost than Grade 316.
Grade 201 stainless steel might be considered for extremely tight budgets, but only for locations that experience minimal salt exposure. However, choosing a lower grade will likely result in higher maintenance costs and shorter service life.
Another notable option for coastal infrastructure is 17-4 stainless steel round bar, particularly for specific components requiring high strength and corrosion resistance. While not typically used for entire barrier systems, 17-4 PH round bars are excellent for:
- Fastening systems
- Support posts
- Structural connectors
- High-stress mounting points
17-4 PH offers unique advantages in these applications:
- Superior mechanical strength (up to twice that of Grade 316)
- Good corrosion resistance (though not as high as Grade 316)
- Excellent fatigue resistance
- Heat-treatable for various strength levels
However, when using 17-4 PH round bars in coastal settings, they should be used in their H1100 or H1150 heat treatment condition for optimal corrosion resistance, though this comes with slightly lower strength than other heat treatment options.
What Is The Cost Difference Between Various Stainless Steel Grades?
Grade 316 stainless steel typically costs 20-30% more than Grade 304, while Grade 201 can be 40-50% less expensive than Grade 316. However, when considering lifecycle costs, Grade 316 often proves more economical due to its longer service life and reduced maintenance requirements.
A typical highway project using Grade 316 stainless steel barriers might cost more upfront but can last 30-40 years with minimal maintenance, compared to 15-25 years for Grade 304 in similar conditions.
How Can The Lifespan Of Lower-Grade Stainless Steel Be Extended In Coastal Areas?
Regular maintenance is crucial for extending the life of any grade of stainless steel in coastal environments. This includes monthly freshwater washing to remove salt deposits and annual inspections for signs of corrosion or damage.
Protective coatings or treatments can also be applied to lower-grade stainless steel to enhance its corrosion resistance. Electropolishing, for example, can improve the surface finish and increase corrosion resistance by up to 30%. However, these additional treatments add to the initial cost and may need to be reapplied periodically.
What Regular Maintenance Is Required For Coastal Stainless Steel Barriers?
Maintaining stainless steel barriers in coastal environments requires a structured approach. To remove salt deposits, pressure washers should be used to wash the barriers monthly with fresh water, particularly after storms or high-tide events. This simple maintenance step can significantly extend the barriers' life.
Annual inspections should include checking for signs of surface rust, pitting, or crevice corrosion. Any damaged areas should be documented and repaired promptly to prevent the spread of corrosion. Inspecting and tightening any loose fasteners is also important, as movement can create areas where corrosion can take hold.
What Are The Environmental Considerations When Choosing Stainless Steel For Coastal Barriers?
Stainless steel is 100% recyclable, making it an environmentally responsible choice for infrastructure projects. The long lifespan of correctly specified stainless steel means fewer replacements are needed over time, reducing the overall environmental impact of manufacturing and installation.
While the initial production of stainless steel requires significant energy, its durability and recyclability offset this impact over time. Additionally, the minimal maintenance requirements mean fewer chemical cleaners and treatments are needed throughout its lifetime, reducing the environmental impact of ongoing maintenance activities.
The carbon footprint can be further reduced by sourcing stainless steel from manufacturers who use electric arc furnaces powered by renewable energy, a growing trend in the industry.
Making The Right Choice For Your Coastal Project
When planning a coastal barrier installation or replacement project, start by getting quotes for both Grade 316 and Grade 304 stainless steel options, including lifecycle cost analysis in your calculations. This comparative approach will help you make a data-driven decision that balances initial costs against long-term maintenance requirements and expected service life while ensuring the safety and durability of your infrastructure project. Remember that choosing a higher grade initially often proves more economical over the full lifespan of the installation.
Image credit: Depositphotos